FEM模拟
FEM分析技术打开了冷弯成形的无限可能性。
目前,冷弯成形仍然极大程度地依赖于操作人员的经验。但是,焊管辊弯成形涉及到复杂的三维弹塑性大变形,仅仅依赖经验丰富的操作人员,对如此复杂的成形过程,应力应变状态的把握和理解是非常有限的,而且如果不通过实际的成形试验,也很难评估成形机组设计的好坏,因此,对工艺的优化变得非常困难,在轧机制造完毕后往往还需要进行多次的设计变更和设备改造。
计算机仿真工艺优化
中田制作所独自开发的三维弹塑性大变形仿真系统可以使我们能够从理论上科学地分析材料的复杂成形。我们建立的辊弯成形仿真系统可以精确地预测材料在轧辊作用下的变形情况,从而使得通过计算机仿真优化辊弯成形工艺成为可能。
计算机上的仿真系统
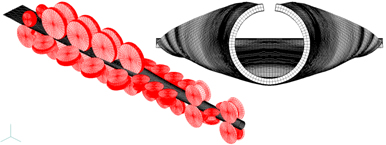
理想的成形方法开发所不可或缺的技术
中田制作所应用FEM分析技术,采用独特的渐开线辊(FF轧辊)开发出理想的成形方法。这一革命性的方法不但完全消除了换辊操作,而且在确定最佳的边缘形状时可以将产品外径、材料厚度和材料种类的影响降到最低。应用FFX成形机组能够制造出诸如X80和N80之类高等级钢管。
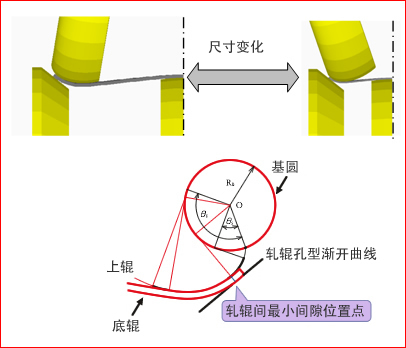
基于FEM分析技术的设计开发
1)机械设计支援
通过FEM成形分析获得的高精度成形载荷数据进一步导入构造分析FEM模型,通过进行构造分析,设计适宜的机械构造。中田制作所在设计中融入独有的Know-how知识,设计出具有高刚度的交叉梁机构牌坊的轧机。
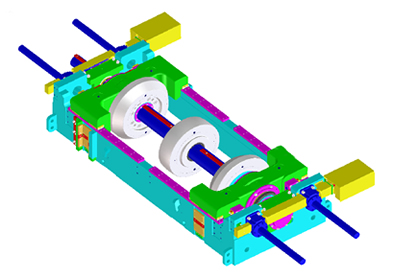
过去由轧辊轴承受的成形荷重现在由交叉梁机构牌坊承担,实现了轧机的高刚度化。这种结构适用于所有粗成形机架,提高了构造的模块化,共用化。
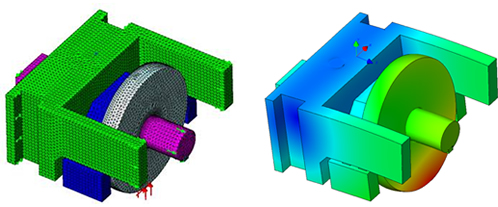
2)助力方矩形管成形技术的开发
通常,通过辊弯成形进行“圆成方”成形制造方矩形管时往往必须需要多段的设备及轧辊群。我们通过有效利用FEM分析技术,实现了轧辊辊型的兼用化,在将换辊数目减少了一半的同时,通过采用全轧辊驱动方式增强推力,提高了成形的稳定性。
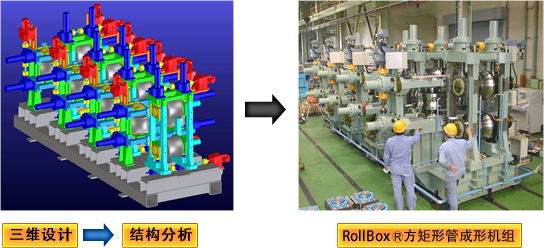
应用于传统型成形机诊断
中田制作所的FEM分析技术在提高产品质量和成材率方面效果显著。